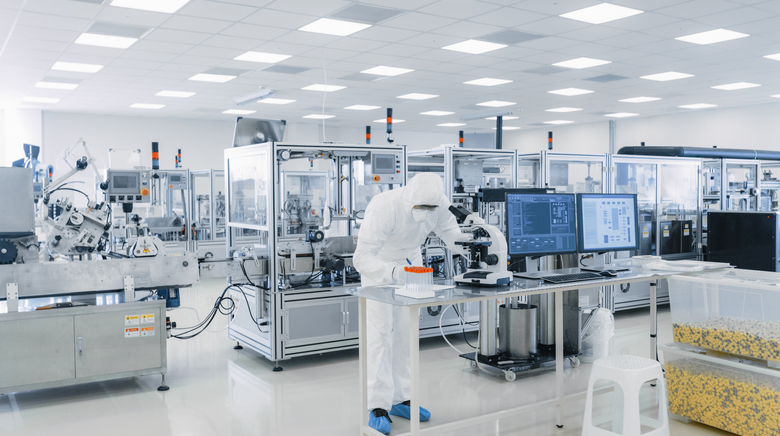
Some Korean biopharmaceutical companies, including LG Chem, Hanmi Pharmaceutical, and Daewoong Bio, are considering introducing the continuous manufacturing (CM) process, attracting the industry’s attention.
Unlike the existing “batch-type” production, continuous manufacturing (CM) is a method of manufacturing products by continuously supplying and processing raw materials without interruption. It reduces production costs by eliminating the need to stop and process drug production in stages.
Continuous manufacturing is new even to the global pharmaceutical industry. Since the U.S. Food and Drug Administration (FDA) and the European Medicines Agency (EMA) first approved Vertex Pharmaceuticals' cystic fibrosis drug Orkambi (lumacaftor-ivacaftor) as a continuous manufacturing drug in 2015, eight drugs have won approval from global regulators as of May.
Nevertheless, the growth of the continuous manufacturing market will likely be steep due to the advantages of reducing production costs.
According to a report "Benefits and Opportunities of Continuous Manufacturing Processes for Pharmaceuticals," published by the KoreaBIO in May, the global market for continuous manufacturing of pharmaceuticals is estimated to be worth $1.59 billion (about 2.09 trillion won) in 2022, with a compound annual growth rate (CAGR) of 17.2 percent through 2028.
"Continuous manufacturing is an old story in the food industry," said Won Kwon-yeon, a Daegu Catholic University College of Pharmacy professor who serves as the Korean Society of Pharmaceutical Science and Technology president. “For example, to make ramen or bread, continuously adding flour and sugar, mixing, kneading, and drying them can be seen as continuous manufacturing."
The production of pharmaceuticals is done from a more conservative perspective, where one manufacturing unit is set up in advance. To determine conformance, Won added each batch is checked step by step, including raw material quality control, manufacturing process control, and finished product quality control.
"The benefits to companies of adopting a continuous pharmaceutical manufacturing process are clear. It is easy to mass produce. Once the raw materials are injected, the drug continues to be produced along the manufacturing process,” he said. “However, the challenge is checking each process step in continuous manufacturing.”
The U.S. Food and Drug Administration has approved only oral solid drugs for continuous manufacturing because it is the formulation that poses the lowest risk to humans in the event of a quality problem, showing the agency's cautious attitude toward continuous manufacturing, Won explained.
"Continuous manufacturing requires less manpower than conventional batch production to reduce labor costs for companies," said Professor Na Dong-hee of Chung-Ang University College of Pharmacy. "There are drugs that do not have much margin left after production. For such products, lowering the unit cost of production will be an important factor."
As most academics cite institutional uncertainty as one of the challenges to introducing CM, the Ministry of Food and Drug Safety (MFDS) is on the verge of issuing guidelines for continuous manufacturing processes. It will be the first regulatory agency worldwide to issue such guidelines since the International Conference on Harmonization of Medicinal Products (ICH) issued them in March.
The ministry launched the public-private drug review communication channel, CHORUS, in March and plans to enact the continuous manufacturing process guidelines in October based on the findings of the Advanced Quality Review Division. More details will be revealed at a briefing session for the Drug Review Division next Tuesday.
About 10 companies are participating in the subcommittee, of which half are pharmaceutical companies. LG Chem and Hanmi Pharmaceutical are especially active. They are also positive in introducing continuous manufacturing processes.
"There is a company in Korea that wants to introduce a continuous manufacturing process, so we have been holding intensive consultations this year," said Park Yoon-joo, head of the National Institute of Food and Drug Safety Evaluation (NIFDS), at a recent meeting with journalists covering the ministry. “During communication, the company has also been setting up the CM process.”
In addition to the companies participating in the Advanced Quality Review Subcommittee, Daewoong Bio, a subsidiary of Daewoong Group, has also made its introduction of CM official.
Selected for the “World Class Plus” program by the Ministry of Trade, Industry, and Energy in July, Daewoong Bio will receive research support to advance its continuous manufacturing process technology. The company plans to use continuous manufacturing to produce enavogliflozin, the main ingredient of its domestic diabetes treatment drug Envlo.
Concerns and expectations coexist as Korean companies attempt to introduce continuous manufacturing processes and the regulator finishes related systems.
"To introduce a continuous manufacturing process, Process Analytical Technology (PAT), which enables real-time quality monitoring, must be established, taking a lot of money, effort, and time," Professor Won said. “However, if we proactively lay the groundwork in Korea, another success story like biosimilars could emerge."